Projects/ Energetic industry
Automated controlling system reconstruction for turbine set № 11
Customer : Client: "AES CHP (Ust – Kamenogorsk Central Heating Plant)"
Automation object description
Т-100-130 steam turbine of Uralsk turbine motor factory with nominal power = 100 000 kW at 3000 rpm, with steam condensation and two- stage network water heating is designated direct drive of hydrogen cooled ТВФ(TVF)-60-2 AC generator with the capacity 100 000 kilowatt . Nominal total value of heating takeoff is160 MMkcal/hr / 310 t/h.
After the modernization in 2013 when the high-pressure cylinder was changed and the intermediate pressure cylinder was modernized and a new excitation system was set, the power of the turbine set has been increased up to 120 megawatt. The turbine set was also provided with electrohydraulic system of regulating and protection (ESRP).
The turbine is intended to operate under live steam with pressure of 130 atm. and temperature of 550ºС, taken before automatic shutoff valve. The calculated temperature of the cooling water at the input to condenser is 20ºС. Nominal value of cooling water is 16000 m3/h.
Automation system purpose
The main purpose of the automation system is to provide efficient control and management of the technological process using the programs of automatic regulators and performing the functions of automatic protection. The automation system that was put onto operation was elaborated instead of the previous old control system.
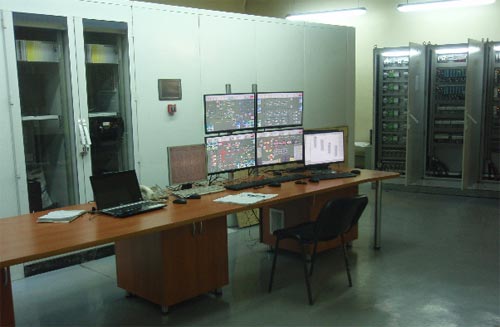
Group control panel: the workplace of the turbine set engine operator
The main functions of the systems are:
- technological information display as symbolic circuits with different refinement degree;
- signaling and registration the messages of exceeding the emergency, warning and technological limits;
- technological data and parameters, system messages long-term archiving;
- reporting documents making;
- system operability diagnosing;
- providing connection and control of electrohydraulic system of regulating and protection (ESRP) elaborated by ООО «НПФ «Ракурс»;
- performing functions of technological protection to switch off the turbine set and high-pressure preheater;
- performing functions of technological blocking to decrease oil pressure in the lubrication system and hydrogen seal of the generator;
- performing functions of technological blocking to increase the levels in the boilers ОБ-1 and ОБ-2, to decrease pressure in the high-pressure preheater ПВД-5 and increasing the pressure level in low-pressure preheater ПНД-2;
- performing functions of АВР condensate transfer pump (CTP) and condensate boiler pumps (CBP);
- automatic keeping the condensate level in the condenser;
- automatic keeping the condensate level in the low-pressure preheater ПНД-1… ПНД-4;
- automatic keeping the condensate level in the low-pressure preheater ПНД-5… ПНД-7;
- automatic keeping the condensate level in the peak boilers ПБ-7..ПБ-9;
- automatic keeping the condensate level in the boilers ОБ-1 и ОБ-2;
- automatic keeping the steam level in the seals header;
- automatic keeping the steam before the steam ejectors;
- automatic keeping the steam after РОУ-10..РОУ-12;
- automatic keeping the steam temperature after РОУ-10..РОУ-12.
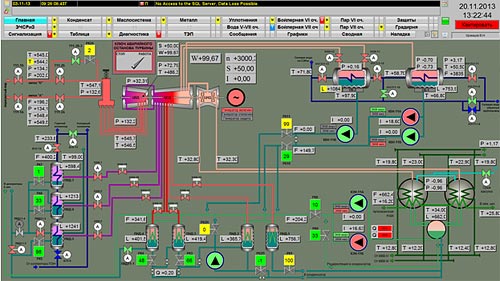
The main symbolic circuit of the turbine set
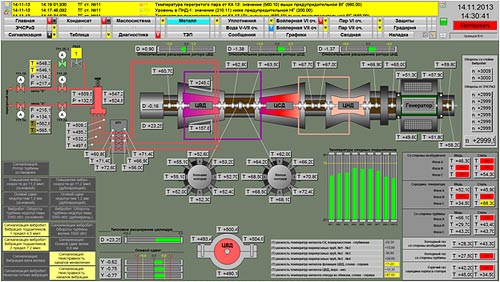
symbolic circuit – temperature control of the turbine set
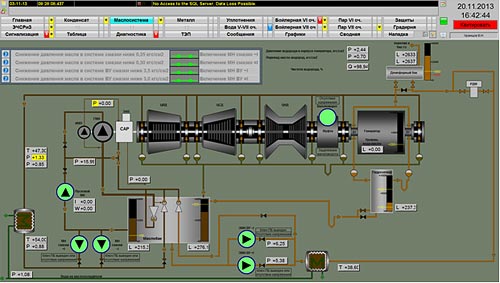
symbolic circuit: turbine set oil system
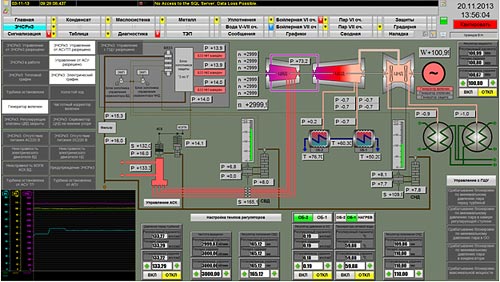
Symbolic circuit: ESRP
The automation system also includes the control paths to control the technological equipment in the boiler station of the VII level:
- automatic keeping the condensate level in the high-pressure preheater ПВД-12-1 and ПВД-12-2;
- automatic keeping the condensate level in the peak boilers ПБ-10..ПБ-15;
- automatic keeping the condensate level in the condensate coolers ОК-1..ОК-3;
- automatic keeping the condensate level in the boiler;
- automatic keeping the steam level after РОУ-14..РОУ-18;
- automatic keeping the temperature level after РОУ-14..РОУ-18;
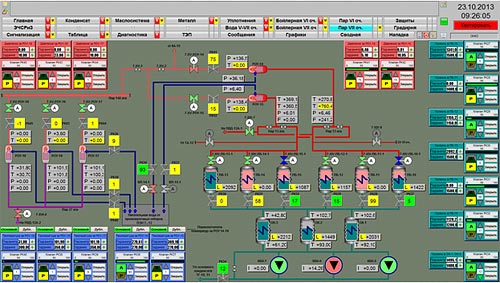
Symbolic circuit :steam of the VII level
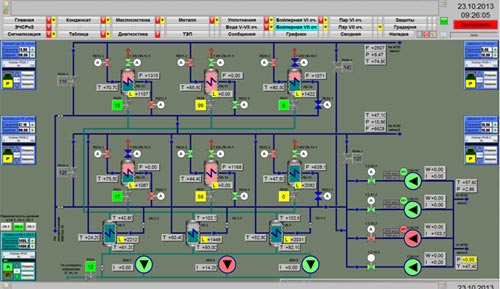
Symbolic circuit: boiler of the VII level
The system structure
The lower level of the system for each of the units is designed on the base of reserved controller S7-416-5H with input/output stations ET200M, that collect and process the technological parameters and control actuators. Input/ output stations ET200M are performed with the function of “emergency replacement”, i.e. have a possibility to replace the functional modules without switching off the controller and interrupting the technological process. The communication between the controller and input/ output stations ET200M is carried out via the reserved network PROFIBUS DP. The communication with the remote input/ output stations ET200M is carried out via the network PROFIBUS DP.
The upper level of the system is a reserved server PCS7 OS Server Redundancy which is supplied with the operator’s workplace №1 and №2. Each of the workstations is supplied with two displays with 23’’ diagonal.
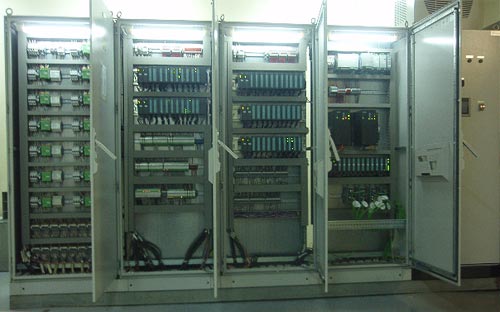
Control cubicles of automated controlling system turbine set
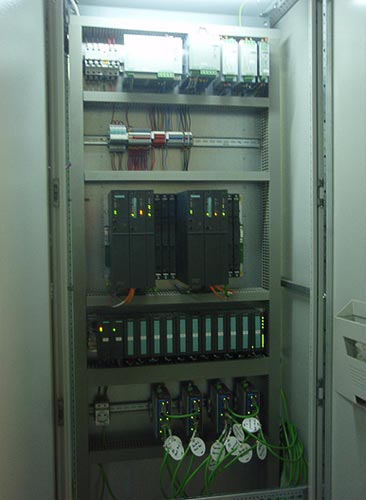
Control cubicle with the reserved controller S7-416-5H
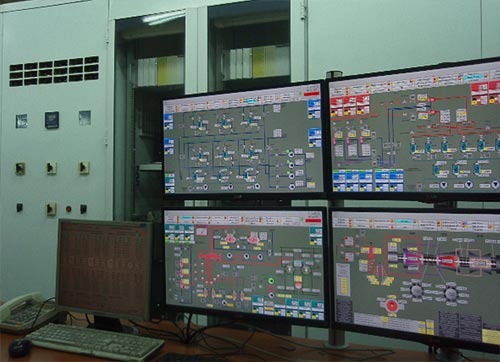
The turbine set operator’s workplace
Elaboration of the software and technical details of the project Automation system is carried out from the Engineering station of the automation system.
The communication between the controller S7-400H and the server database is carried out via the reserved network Industrial Ethernet “electric ring” with the capacity up to 100megabit/sec. The communication with the operator’s workplace and the server is carried out via terminal net Industrial Ethernet.
Data transporting to the technological net of «AES Ust-Kamenogorsk HPP» ltd.is carried out by means of OPC technology.
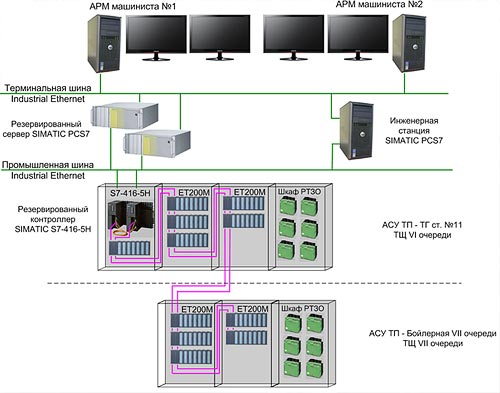
Complex Technical Means Structure Scheme
The time of the project realization
Elaboration : December 2012 – March 2013
Delivery of cubicles and controlling equipment and software – March- May 2013
Mounting – March-May 2013
Starting-up and adjustment – October-November 2013
Automatic regulations ant testing – November 2013
Putting into operation – 22 November 2013 |